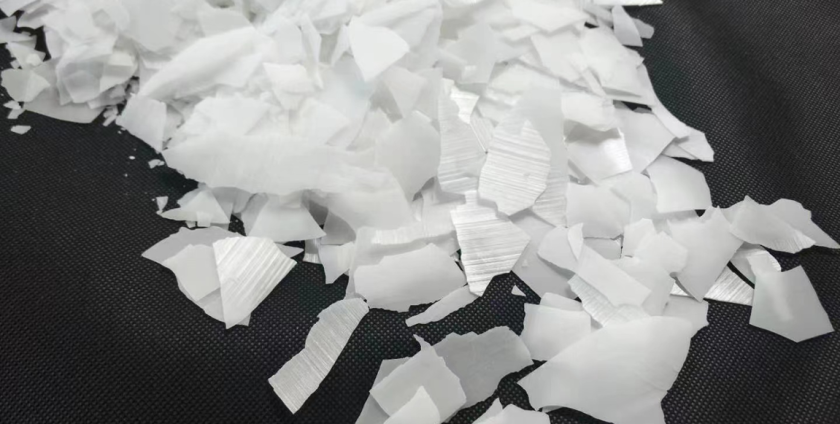
Polyethylene Wax & Its Uses in Different Industries
Polyethylene wax (PE wax) is a versatile material widely used across various industries due to its unique properties. It is a type of synthetic wax derived from ethylene, a byproduct of petroleum. Its high molecular weight, chemical resistance, and excellent thermal stability make it a valuable ingredient in numerous applications. This blog will explore what polyethylene wax is, its production process, various types, uses in different industries, advantages and disadvantages, future prospects, and why Peak Universal Business is the ideal supplier for your PE wax needs. (Polyethylene Wax Uses in Different Industries: Plastic and Polymer Industry, Coatings and Paints, Adhesives and Sealants, Rubber and Tire Industry, Printing Inks, Textile Industry, Cosmetics and Personal Care, Candles)
What is Polyethylene Wax?
Polyethylene wax is a low molecular weight polymer derived from ethylene, produced through the polymerization process of ethylene or as a byproduct of polyethylene production. It is characterized by its excellent hardness, low viscosity, and high melting point, which contribute to its widespread use in various industrial applications.
Chemical Composition and Physical Properties of Polyethylene Wax
PE wax primarily consists of long-chain hydrocarbons with the following key properties:
- High Melting Point: Typically ranges between 100°C and 140°C.
- Low Viscosity: Enhances its ease of application in various formulations.
- Chemical Resistance: Resistant to acids, bases, and other chemicals.
- Thermal Stability: Can withstand high temperatures without degradation.
- Hardness: Provides durability and abrasion resistance.
Types of Polyethylene Wax
1. Low-Density Polyethylene (LDPE) Wax
- Produced from low-density polyethylene, characterized by flexibility and low melting point.
- Used in applications requiring lower melting temperatures and more flexibility.
2. High-Density Polyethylene (HDPE) Wax
- Derived from high-density polyethylene, known for its higher melting point and hardness.
- Suitable for applications requiring higher thermal stability and abrasion resistance.
3. Oxidized Polyethylene Wax (OPE Wax)
- Modified by introducing oxygen into the polymer chain, improving its adhesion and compatibility with other materials.
- Commonly used in coatings, inks, and adhesives.
4. Functionalized Polyethylene Wax
- Chemically modified to introduce functional groups, enhancing compatibility with specific polymers and resins.
- Used in specialized applications requiring unique properties.
Production Process of Polyethylene Wax
Polyethylene wax is typically produced through one of the following methods:
1. Polymerization Process
- Ethylene gas is polymerized under specific conditions to produce low molecular weight polyethylene.
- The process involves the use of catalysts and controlled temperature and pressure to achieve the desired molecular weight.
2. Thermal Cracking
- High molecular weight polyethylene is thermally cracked to produce low molecular weight wax.
- This process involves heating the polymer to high temperatures, causing the long chains to break down into shorter chains.
3. Modification and Functionalization
- Oxidation or grafting processes are used to introduce functional groups or improve the properties of the wax.
- These modifications enhance the wax’s performance in specific applications.
Uses of Polyethylene Wax in Different Industries
Polyethylene Wax Uses in Different Industries: Plastic and Polymer Industry, Coatings and Paints, Adhesives and Sealants, Rubber and Tire Industry, Printing Inks, Textile Industry, Cosmetics and Personal Care, Candles
1. Plastic and Polymer Industry
- Lubricant and Release Agent: PE wax is used as a lubricant and mold release agent in plastic processing, reducing friction and preventing adhesion to molds.
- Improved Flow Properties: Enhances the flow properties of polymer melts, facilitating smoother extrusion and molding processes.( Plastic and Polymer Industry)
- Masterbatch Production: Acts as a dispersing agent for pigments and additives in masterbatches, ensuring uniform distribution.
2. Coatings and Paints
- Surface Modifier: PE wax is added to coatings and paints to improve surface properties such as scratch resistance, gloss, and water repellency.
- Matting Agent: Used as a matting agent to achieve desired surface finishes, reducing gloss levels.
- Anti-Blocking Agent: Prevents the sticking of coated surfaces, improving handling and application.
3. Adhesives and Sealants
- Hot Melt Adhesives: PE wax is a key ingredient in hot melt adhesives, enhancing adhesion properties and thermal stability.
- Improved Flexibility: Enhances the flexibility and toughness of adhesive formulations, ensuring better performance.? (Adhesives and Sealants)
- Sealant Formulations: Used in sealants to improve adhesion and durability, particularly in high-temperature environments.(Adhesives and Sealants)
4. Rubber and Tire Industry
- Processing Aid: Acts as a processing aid in rubber compounding, improving the dispersion of fillers and additives.
- Release Agent: Used as a release agent in tire manufacturing, preventing rubber from sticking to molds.
- Enhanced Durability: Improves the wear resistance and durability of rubber products. (Rubber and Tire Industry)
5. Printing Inks
- Rheology Modifier: PE wax is used to modify the rheology of printing inks, improving flow properties and stability.
- Abrasion Resistance: Enhances the abrasion resistance and durability of printed surfaces.
- Gloss and Finish: Contributes to the gloss and finish of printed materials, ensuring high-quality prints.
6. Textile Industry
- Softening Agent: Used as a softening agent in textile processing, providing a smooth and soft finish to fabrics.
- Lubricant: Acts as a lubricant in textile fibers, reducing friction during processing.
- Water Repellency: Enhances the water repellency of textile products, improving their performance in outdoor applications.
7. Cosmetics and Personal Care
- Thickening Agent: Used as a thickening agent in cosmetic formulations, providing texture and consistency.
- Emollient: Acts as an emollient, providing a smooth and silky feel to skin care products.
- Stability: Improves the stability and shelf life of cosmetic products.
8. Candles
- Enhances Burning Properties: PE wax is added to candles to improve burning properties, ensuring a steady and consistent flame.
- Mold Release: Facilitates easy release of candles from molds, ensuring smooth and finished products.
- Gloss and Finish: Contributes to the gloss and appearance of candles, enhancing their aesthetic appeal.
Advantages of Using Polyethylene Wax
1. Versatility
- PE wax can be used in a wide range of applications across various industries, making it a versatile and valuable material.
2. Cost-Effective
- Provides cost-effective solutions for improving product performance and properties.
- Reduces production costs by enhancing processing efficiency and reducing waste.
3. Improved Performance
- Enhances the performance of products, including durability, resistance to wear, and thermal stability.
4. Compatibility
- Compatible with various polymers, resins, and other materials, facilitating easy integration into existing formulations.
5. Environmental Benefits
- PE wax is often derived from byproducts of petroleum refining, contributing to waste reduction and sustainable practices.
Disadvantages of Using Polyethylene Wax
1. Limited Biodegradability
- PE wax is not biodegradable, posing environmental concerns if not disposed of properly.
2. Processing Challenges
- Requires careful handling and processing to achieve the desired properties and performance.
3. Potential Health Risks
- Inhalation of PE wax fumes during processing can pose health risks, requiring appropriate safety measures.
Future Prospects of Polyethylene Wax
The future of polyethylene wax looks promising, with ongoing research and development focused on optimizing its properties and discovering new applications. Emerging trends and technologies include:
1. Sustainable and Biodegradable Alternatives
- Development of sustainable and biodegradable alternatives to traditional PE wax, addressing environmental concerns.
2. Advanced Formulations
- Creation of advanced formulations with enhanced properties, such as improved compatibility and performance.
3. Expanding Applications
- Exploration of new applications in emerging industries, including renewable energy, electronics, and advanced manufacturing.
4. Global Market Growth
- Increasing demand for PE wax in developing markets, driven by industrial growth and technological advancements.
Price Factors for Polyethylene Wax
1. Raw Material Costs
- Prices of raw materials, including ethylene and other petroleum derivatives, influence the cost of PE wax.
2. Production Costs
- Costs associated with polymerization, processing, and modification of PE wax impact pricing.
3. Supply and Demand
- Market demand and supply dynamics, including seasonal variations and industry trends, affect prices.
4. Quality and Purity
- Higher quality and purity levels command higher prices, reflecting the value of consistent performance and properties.
Peak Universal Business as Your Polyethylene Wax Supplier
Choosing Peak Universal Business as your supplier for polyethylene wax ensures you receive high-quality products that meet industry standards. With a reputation for reliability and excellence, Peak Universal Business provides PE wax that enhances the performance of products across various industries. Their expertise in sourcing and supplying PE wax makes them a preferred partner for innovative solutions.
Why Choose Peak Universal Business?
1. Quality Assurance
- Committed to providing high-quality PE wax that meets stringent industry standards.
- Thorough testing and quality control processes ensure product consistency and reliability.
2. Expertise and Experience
- With years of experience in the industry, Peak Universal Business has a deep understanding of PE wax’s applications and benefits.
- Their team of experts can provide technical support and guidance for your specific needs.
3. Global Reach
- A robust supply chain that ensures timely delivery of PE wax worldwide.
- Their global network enables them to meet the demands of clients across various regions.
4. Customer-Centric Approach
- Prioritizes customer satisfaction and strives to build long-term relationships with their clients.
- Offers customized solutions and flexible pricing options to meet your project requirements.
Conclusion
Polyethylene wax is a versatile and valuable material widely used across various industries for its unique properties and performance benefits. From plastic processing and coatings to adhesives, rubber, and cosmetics, PE wax enhances the quality and functionality of products. Despite some challenges, its future prospects look bright, with ongoing research and development focused on sustainability and advanced formulations. For top-quality polyethylene wax, trust Peak Universal Business as your reliable supplier, ensuring you get the best product for your needs.
📣 Call to Peak Universal Business
🔍Looking for High-Performance Polyethylene Wax for Your Industry?
We in Peak Universal Business, supply PE Wax in powder, flake, and emulsion forms, customized for plastic, coating, ink, and adhesive industries.
We supply:
-
✔️ Oxidized and non-oxidized PE wax
-
✔️ Flakes, powder, granules, and emulsions
-
✔️ Technical support for custom formulations
-
✔️ Bulk packaging and international shipping
🛒 Request a Quote Today
📧 Email: [email protected]
📞 Phone: +971 4 878 2031
PUBLtd as your Polyethylene Wax Supplier. Our Expert will be in touch with you to guide you about the Use of PE Wax that can be produced according to your project requirements. If You have any other Query or Question you want to ask, Please don’t hesitate to Contact Us.
- 0 comment
Leave a Reply