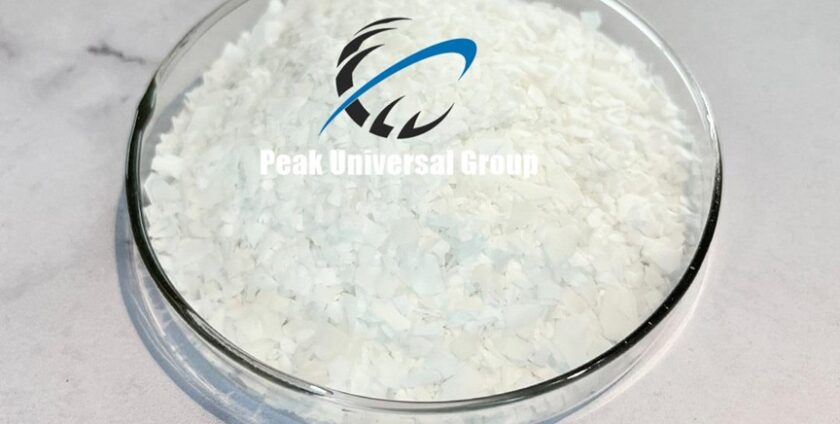
Polyethylene Wax (PE Wax): Manufacturing, Uses, Applications, and Benefits
Polyethylene Wax (PE wax) is a versatile and essential material used in a variety of industries due to its unique properties and benefits. This blog will explore the intricate details of how PE wax is manufactured, its extensive uses, applications, and benefits. We will also highlight Peak Universal Business as a reliable supplier of PE wax. (Manufacturing of Polyethylene Wax: Polymerization of Ethylene, Thermal Cracking of High-Density Polyethylene (HDPE), High-Pressure Polymerization, Modification of Polyethylene)
What is PE Wax?
Polyethylene wax, commonly known as PE wax, is a low molecular weight polyethylene polymer. It is a type of synthetic wax derived from ethylene, the simplest olefin, through polymerization. PE wax is known for its excellent thermal stability, hardness, and low viscosity, making it suitable for various industrial applications.
Chemical Composition
PE wax is composed of long chains of carbon and hydrogen atoms, with the general chemical formula (C₂H₄) n. The molecular weight and chain length can vary, influencing its physical properties and suitability for different applications.
Physical Properties
- Color: White or slightly yellow
- Odor: Odorless
- Melting Point: 85-140°C (185-284°F), depending on the grade.
- Density: 0.90-0.98 g/cm³
- Solubility: Insoluble in water, soluble in organic solvents like toluene, xylene, and some chlorinated hydrocarbons
- Viscosity: Low viscosity, which varies with molecular weight
Manufacturing of Polyethylene Wax (PE Wax)
(Polymerization of Ethylene, Thermal Cracking of High-Density Polyethylene (HDPE), High-Pressure Polymerization, Modification of Polyethylene)
Production Methods
PE wax can be produced using several methods, each yielding waxes with different properties suitable for various applications. The most common production methods include:
- Polymerization of Ethylene
- Thermal Cracking of High-Density Polyethylene (HDPE)
- High-Pressure Polymerization
- Modification of Polyethylene
1. Polymerization of Ethylene
Polymerization of Ethylene– In this method, ethylene gas is polymerized under controlled conditions using catalysts. The polymerization process can be conducted at high or low pressures, resulting in different types of polyethylene wax.
- High-Pressure Polymerization: This process involves the polymerization of ethylene at high pressures (1500-3000 atm) and high temperatures (200-300°C). The resulting PE wax has a low molecular weight and a broad molecular weight distribution.
- Low-Pressure Polymerization: This process uses Ziegler-Natta or metallocene catalysts at lower pressures and temperatures. The resulting PE wax has a narrower molecular weight distribution and more consistent properties.
2. Thermal Cracking of High-Density Polyethylene (HDPE)
Thermal Cracking, or pyrolysis, involves breaking down HDPE into smaller molecules by heating it to high temperatures (400-500°C) in the absence of oxygen. This process produces low molecular weight PE wax with a high degree of crystallinity and hardness.
3. High-Pressure Polymerization
High-Pressure Polymerization– This method involves polymerizing ethylene at very high pressures (up to 3000 atm) and temperatures (200-300°C). The resulting PE wax has a unique structure with a broad molecular weight distribution, making it suitable for specific applications.
4. Modification of Polyethylene
Modification of Polyethylene– Existing polyethylene can be chemically or physically modified to produce PE wax. Chemical modification includes processes like oxidation or chlorination, while physical modification involves mechanical processes like milling or grinding to reduce the polymer’s molecular weight.
Refining and Processing
Refining and Processing- After production, PE wax undergoes refining and processing to enhance its properties and make it suitable for various applications. This includes:
- Purification: Removing impurities to improve the wax’s color and consistency.
- Pelletizing: Converting the wax into pellets for easier handling and use in manufacturing processes.
- Blending: Mixing different grades of PE wax to achieve specific properties required for particular applications.
Uses and Applications of Polyethylene Wax (PE Wax)
PE wax’s unique properties make it suitable for a wide range of applications across various industries. Below are some of the most common uses and applications of PE wax:
1. Plastics and Polymers
PE wax is widely used in the plastics and polymer industry as a processing aid and additive. It improves the processing characteristics and properties of plastic products.
Applications in Plastics and Polymers
- Lubricant: PE wax acts as a lubricant in the extrusion and molding of plastics, reducing friction and wear on machinery and improving the flow of polymer melts.
- Dispersing Agent: It helps in the dispersion of fillers, pigments, and other additives in plastic formulations, ensuring uniform distribution and enhancing the final product’s appearance and performance.
- Mold Release Agent: PE wax is used as a mold release agent to prevent plastic parts from sticking to molds during the manufacturing process, facilitating easy removal and reducing defects.
- Impact Modifier: It enhances the impact resistance and toughness of plastic products, making them more durable and less prone to breakage.
2. Coatings and Paints
PE wax is used in coatings and paints to improve surface properties and enhance performance.
Applications in Coatings and Paints
- Scratch and Mar Resistance: PE wax enhances the scratch and mar resistance of coatings, providing a durable and long-lasting finish.
- Gloss Control: It helps in controlling the gloss level of coatings, enabling the production of matte or semi-gloss finishes as required.
- Slip and Rub Resistance: PE wax improves the slip and rub resistance of coatings, making surfaces smoother and more resistant to wear and abrasion.
- Anti-Blocking: It prevents coated surfaces from sticking together, ensuring easy handling and storage of coated materials.
3. Adhesives and Sealants
PE wax is an essential component in adhesives and sealants, where it enhances performance and application properties.
Applications in Adhesives and Sealants
- Hot Melt Adhesives: PE wax improves the viscosity and thermal stability of hot melt adhesives, ensuring smooth application and strong bonding.
- Pressure-Sensitive Adhesives: It enhances the tackiness and adhesion properties of pressure-sensitive adhesives, making them more effective in bonding various substrates.
- Sealants: PE wax provides flexibility, durability, and resistance to environmental factors in sealants, ensuring long-lasting sealing performance.
4. Rubber and Tires
In the rubber industry, PE wax is used as a processing aid and additive to improve the properties of rubber products.
Applications in Rubber and Tires
- Processing Aid: PE wax reduces the viscosity of rubber compounds, making them easier to process and mold into desired shapes.
- Release Agent: It acts as a release agent, preventing rubber products from sticking to molds during the manufacturing process and ensuring easy removal.
- Anti-Ozonant: PE wax provides protection against ozone degradation, extending the lifespan of rubber products exposed to outdoor environments.
- Filler Dispersion: It aids in the uniform dispersion of fillers and other additives in rubber compounds, enhancing the overall quality and performance of rubber products.
5. Printing Inks
PE wax is used in printing inks to improve print quality and performance.
Applications in Printing Inks
- Abrasion Resistance: PE wax enhances the abrasion resistance of printing inks, ensuring that printed materials remain intact and legible even with frequent handling.
- Gloss Control: It helps in achieving the desired gloss level in printing inks, allowing for matte or glossy finishes as required.
- Slip and Rub Resistance: PE wax improves the slip and rub resistance of printing inks, preventing smudging and ensuring sharp, clear prints.
- Improved Flow: It enhances the flow properties of printing inks, ensuring smooth application and consistent print quality.
6. Textiles
PE wax is used in the textile industry for various applications, particularly in fabric finishing and processing.
Applications in Textiles
- Softening Agent: PE wax is used as a softening agent to improve the hand feel and drape of fabrics, making them more comfortable to wear.
- Water Repellence: It imparts water-repellent properties to textiles, making them suitable for outdoor and weather-resistant applications.
- Fabric Finishing: PE wax is used in fabric finishing processes to enhance the appearance, durability, and performance of textiles.
- Stain Resistance: It provides stain resistance to fabrics, making them easier to clean and maintain.
7. Polishes and Cleaners
PE wax is a key ingredient in polishes and cleaners, providing protective and enhancing properties.
Applications in Polishes and Cleaners
- Furniture Polish: PE wax is used in furniture polishes to provide a protective, glossy finish and enhance the appearance of wood surfaces.
- Car Wax: It is used in car wax formulations to protect automotive finishes from environmental damage and provide a high-gloss shine.
- Floor Polish: PE wax is used in floor polishes to protect and enhance the appearance of flooring materials, providing a durable, scuff-resistant finish.
- Metal Cleaners: It is used in metal cleaners and polishes to remove tarnish and oxidation, leaving a protective coating that prevents further corrosion.
8. Packaging
PE wax is used in packaging applications to enhance the performance and durability of packaging materials.
Applications in Packaging
- Coating: PE wax is used as a coating material for paper, cardboard, and other packaging materials to provide moisture resistance and improve durability.
- Heat Sealing: It is used in heat sealing applications to ensure strong, reliable seals in packaging materials, preventing leaks and contamination.
- Anti-Blocking: PE wax prevents packaging materials from sticking together, ensuring easy handling and storage.
- Flexibility: It provides flexibility and durability to packaging materials, making them more resistant to damage during handling and transportation.
Benefits of Using Polyethylene Wax (PE Wax)
PE wax offers numerous benefits across various industries due to its unique properties and versatility. Here are some of the key benefits of using PE wax:
1. Enhanced Processing and Manufacturing Efficiency
PE wax improves the processing and manufacturing efficiency of various materials, including plastics, rubber, and coatings. It acts as a lubricant, reducing friction and wear on machinery, and as a dispersing agent, ensuring uniform distribution of additives and fillers.
2. Improved Product Performance
PE wax enhances the performance of end products by providing properties such as abrasion resistance, scratch resistance, and improved flow. This results in more durable, high-quality products that meet industry standards and consumer expectations.
3. Versatility
PE wax is a highly versatile material that can be used in a wide range of applications across various industries. Its ability to enhance different properties makes it a valuable additive in plastics, coatings, adhesives, textiles, and more.
4. Cost-Effectiveness
Using PE wax can lead to cost savings in manufacturing processes by improving efficiency, reducing defects, and extending the lifespan of machinery and end products. Its versatility also means that a single material can be used for multiple applications, reducing the need for multiple additives.
5. Environmental Benefits
PE wax is a synthetic material that can be produced and used in environmentally friendly ways. Its use in applications such as coatings and adhesives can reduce the need for volatile organic compounds (VOCs) and other harmful chemicals, contributing to a healthier environment.
Peak Universal Business: Your Trusted Supplier of Polyethylene Wax (PE Wax)
Peak Universal Business is a leading supplier of high-quality polyethylene wax (PE wax) for various industries. With a commitment to excellence and customer satisfaction, they offer a wide range of PE wax products tailored to meet the specific needs of their clients.
Why Choose Peak Universal Business?
- Quality Assurance: Peak Universal Business ensures the highest quality standards in their PE wax products, guaranteeing consistency and reliability.
- Technical Expertise: Their team of experts provides technical support and guidance, helping customers optimize the use of PE wax in their applications.
- Customized Solutions: They offer customized PE wax solutions to meet the unique requirements of different industries and applications.
- Sustainability Focus: Peak Universal Business is committed to sustainability and environmentally responsible practices in the production and supply of PE wax.
Conclusion
Polyethylene wax (PE wax) is a versatile and valuable material with a wide range of uses and applications across various industries. Its unique properties, such as low viscosity, thermal stability, and hardness, make it suitable for enhancing the performance of plastics, coatings, adhesives, rubber, and more. The manufacturing process of PE wax involves several methods, each yielding waxes with different properties.(Manufacturing of Polyethylene Wax: Polymerization of Ethylene, Thermal Cracking of High-Density Polyethylene (HDPE), High-Pressure Polymerization, Modification of Polyethylene)
Peak Universal Business stands out as a reliable supplier of high-quality PE wax, offering technical expertise, customized solutions, and a commitment to sustainability. By understanding the properties, production process, and diverse applications of PE wax, manufacturers can make informed decisions to enhance their products and processes, ultimately achieving greater success in their industries.
📣 Call to Peak Universal Business
🔍Looking for High-Performance Polyethylene Wax for Your Industry?
We in Peak Universal Business, supply PE Wax in powder, flake, and emulsion forms, customized for plastic, coating, ink, and adhesive industries.
We supply:
-
✔️ Oxidized and non-oxidized PE wax
-
✔️ Flakes, powder, granules, and emulsions
-
✔️ Technical support for custom formulations
-
✔️ Bulk packaging and international shipping
🛒 Request a Quote Today
📧 Email: [email protected]
📞 Phone: +971 4 878 2031
PUBLtd as your Polyethylene Wax Supplier. Our Expert will be in touch with you to guide you about the Use of PE Wax that can be produced according to your project requirements. If You have any other Query or Question you want to ask, Please don’t hesitate to Contact Us.
- 0 comment
Leave a Reply