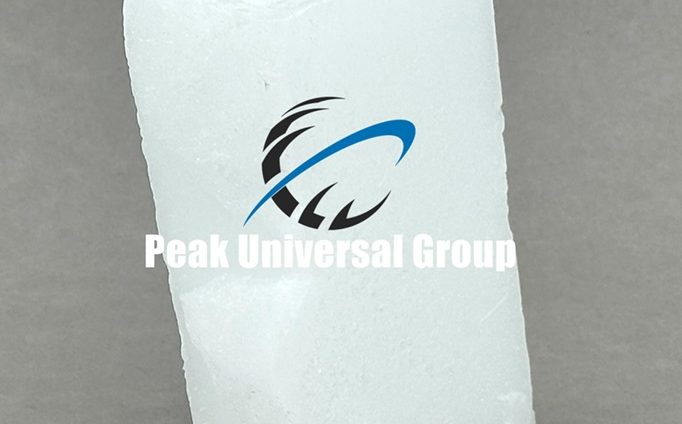
Paraffin Wax: Its Key Properties, Application & Benefits in Rubber Industry
Paraffin wax is a highly versatile material with wide-ranging applications across various industries, including the rubber industry. This blog will delve into the role of paraffin wax in the rubber industry, exploring its benefits, specific applications, Manufacturing Process of Paraffin Wax and why Peak Universal Business is your trusted supplier for this essential material.
What is Paraffin Wax?
Paraffin wax is a white or colorless soft solid derived from saturated hydrocarbons. It is primarily obtained from petroleum, coal, or shale oil. Known for its excellent insulating properties, moisture barrier capabilities, and smooth texture, paraffin wax is an essential material in numerous industrial applications.
Key Properties of Paraffin Wax
1. Melting Point: Typically, between 46°C to 68°C (115°F to 154°F)
2. Density: About 0.9 g/cm³
3. Solubility: Insoluble in water, soluble in ether, benzene, and certain esters
4. Appearance: White, odorless, and tasteless
5. Form: Available in solid blocks, pellets, or flakes
The Role of Paraffin Wax in the Rubber Industry
Paraffin wax plays a crucial role in the rubber industry, where it is used as a key ingredient in the manufacture of various rubber products. Its unique properties make it an indispensable component in rubber processing.
Benefits of Paraffin Wax in Rubber Applications
1. Anti-Ozonant Properties: Paraffin wax forms a protective layer on the surface of rubber products, preventing degradation caused by ozone exposure.
2. Improved Processability: It enhances the processability of rubber compounds, making them easier to mold and shape.
3. Enhanced Flexibility: Paraffin wax improves the flexibility of rubber products, making them more durable and resistant to cracking.
4. Reduced Stickiness: It reduces the stickiness of rubber compounds, facilitating easier handling and processing.
5. Moisture Barrier: Provides an effective moisture barrier, protecting rubber products from moisture-related damage.
Specific Applications of Paraffin Wax in the Rubber Industry
Paraffin wax is used in various stages of rubber manufacturing and in a wide range of rubber products. Here are some of the key applications:
1. Tire Manufacturing
One of the primary uses of paraffin wax in the rubber industry is in the manufacturing of tires. Tires are exposed to harsh environmental conditions, including ozone, UV radiation, and temperature fluctuations. Paraffin wax helps protect tires from these factors, ensuring longevity and performance.
Uses:
- Ozone Protection: Paraffin wax migrates to the surface of the tire, forming a protective layer that shields the rubber from ozone attack.
- Flexibility: Enhances the flexibility of the rubber, preventing cracking and extending the tire’s lifespan.
- Processing Aid: Improves the processability of tire compounds, making them easier to mold and shape during manufacturing.
Applications:
- Passenger Vehicle Tires: Used in the production of tires for cars, SUVs, and light trucks.
- Commercial Vehicle Tires: Essential in the manufacturing of tires for trucks, buses, and other commercial vehicles.
- Specialty Tires: Used in the production of specialty tires, including those for agricultural and industrial equipment.
2. Rubber Belts and Hoses
Paraffin wax is also used in the production of rubber belts and hoses, which are critical components in various industrial and automotive applications. These products require high flexibility, durability, and resistance to environmental factors.
Uses:
- Anti-Ozonant: Provides protection against ozone and UV radiation, preventing degradation and extending the life of rubber belts and hoses.
- Flexibility Enhancer: Improves the flexibility and elasticity of rubber compounds, ensuring reliable performance.
- Processing Aid: Facilitates easier handling and processing during manufacturing.
Applications:
- Automotive Belts and Hoses: Used in the production of timing belts, serpentine belts, radiator hoses, and other automotive components.
- Industrial Belts and Hoses: Essential in the manufacturing of conveyor belts, hydraulic hoses, and other industrial equipment.
3. Rubber Seals and Gaskets
Rubber seals and gaskets are used in a wide range of applications to prevent leakage and ensure a tight seal between two surfaces. Paraffin wax is used to enhance the properties of these rubber components.
Uses:
- Ozone Protection: Forms a protective barrier against ozone and other environmental factors.
- Improved Flexibility: Enhances the flexibility and durability of rubber seals and gaskets.
- Processing Aid: Facilitates easier molding and shaping during the manufacturing process.
Applications:
- Automotive Seals and Gaskets: Used in engine components, doors, windows, and other automotive parts.
- Industrial Seals and Gaskets: Essential in machinery, equipment, and piping systems to prevent leaks and ensure reliable operation.
4. Rubber Insulation
Paraffin wax is used in the production of rubber insulation materials, which are used to insulate wires, cables, and other electrical components. These materials require excellent insulating properties and resistance to environmental factors.
Uses:
- Moisture Barrier: Provides an effective moisture barrier, protecting insulation materials from moisture-related damage.
- Insulating Properties: Enhances the insulating properties of rubber compounds, ensuring reliable performance.
- Flexibility Enhancer: Improves the flexibility and durability of rubber insulation materials.
Applications:
- Electrical Wires and Cables: Used to insulate wires and cables in various electrical and electronic applications.
- Industrial Insulation: Essential in insulating machinery, equipment, and piping systems.
The Manufacturing Process of Paraffin Wax
Understanding the Manufacturing Process of Paraffin Wax can provide insights into its quality and properties. Here is an overview of how paraffin wax is produced:
1. Crude Oil Extraction
The production of paraffin wax begins with the extraction of crude oil from oil wells. Crude oil is a complex mixture of hydrocarbons and other organic compounds, which are separated and refined to produce various petroleum products.
2. Distillation
Once the crude oil is extracted, it undergoes a distillation process to separate it into different fractions based on their boiling points. This process takes place in a distillation tower, where the crude oil is heated, and its components are separated into lighter and heavier fractions.
3. Dewaxing
The heavier fractions from the distillation process contain paraffin wax. These fractions are further processed through a dewaxing process to remove the wax. Dewaxing can be done using various methods, including:
- Solvent Dewaxing: In this method, solvents such as methyl ethyl ketone (MEK) or toluene are used to dissolve the oil, leaving the wax behind.
- Pressing: This mechanical method involves pressing the oil to separate the wax.
- Chilling: The oil is chilled to precipitate the wax, which is then filtered out.
4. Refining
The separated wax undergoes refining to remove impurities and enhance its quality. The refining process includes:
- Sweating: A process where the wax is slowly heated to allow the oil to “sweat” out of the wax.
- Hydrogenation: Hydrogen is added to the wax to saturate any unsaturated hydrocarbons, making it more stable.
- Filtering: The wax is filtered to remove any remaining impurities and achieve the desired purity level.
5. Forming and Packaging
Manufacturing Process of Paraffin Wax, After refining, the paraffin wax is formed into the desired shapes, such as blocks, pellets, or flakes. It is then packaged and distributed for various industrial uses.
Why Choose Peak Universal Business as Your Paraffin Wax Supplier?
When it comes to sourcing high-quality paraffin wax for the rubber industry, Peak Universal Business is your trusted partner. Here are some reasons why you should choose them as your supplier:
1. Quality Assurance: Peak Universal Business ensures that their paraffin wax meets stringent quality standards, providing you with reliable and consistent materials.
2. Competitive Pricing: They offer competitive prices without compromising on quality, ensuring you get the best value for your investment.
3. Reliable Supply Chain: With a robust supply chain, Peak Universal Business guarantees timely delivery, ensuring your projects proceed without delay.
4. Expertise and Support: Their team of experts is always available to provide guidance and support, helping you select the right products for your specific needs.
5. Customer Satisfaction: Committed to customer satisfaction, Peak Universal Business offers exceptional service and support, ensuring a seamless procurement experience.
Conclusion
Paraffin wax is an essential material in the rubber industry, offering numerous benefits that enhance the quality and performance of rubber products. From tire manufacturing and rubber belts to seals, gaskets, and insulation materials, paraffin wax plays a crucial role in improving flexibility, durability, and resistance to environmental factors.
Understanding the production process, specific applications, and benefits of paraffin wax can help you make informed decisions when sourcing this vital material. By choosing Peak Universal Business as your supplier, you can be confident in receiving high-quality paraffin wax, competitive pricing, reliable delivery, and expert support.
Whether you need paraffin wax for tire manufacturing, rubber belts and hoses, seals and gaskets, or insulation materials, Peak Universal Business has the expertise and resources to meet your needs. Experience the difference in quality and service by partnering with Peak Universal Business for your paraffin wax requirements.
You can Read More about Paraffin Wax Here:
Slack Wax for Rubber & Tire Industry
What is the role of Rubber Process Oil ?
What is Normal Paraffin & its Uses
If You have any other Query or Question you want to ask, Please don’t hesitate to Contact Us
- 0 comment
Leave a Reply